- 目前炼铟分两种,即原生铟和再生铟。原生铟主要是从原矿中提取铟,也是当前冶炼铟的主要来源。再生铟则是对废弃金属回收后的冶炼,主要是从铅、锌、铜、锡等矿石冶炼过程中回收的副产品,但再生铟占的总量不大。
- 原生铟主要来自矿产,原生铟占的总量很大。尚未发现铟的单独矿床,它以微量伴生在锌、锡等矿物中。当其含量达十万分之几时,就有工业生产价值,目前主要是从闪锌矿中提取。我国闪锌矿主要分布在云南省,云南省已经探明的高铁闪锌矿储量达700万金属吨。
- 目前生产的大多数铟都是从铅、锌、铜、锡等矿石冶炼过程中回收的副产品。在从较难挥发的锡和铜内分离铟的过程中,铟多数富集在烟道灰和浮渣内,在从挥发性的锌和镉中分离铟时,铟则富集于炉渣及滤渣内。我国生产铟主要是从铅、锌冶炼的副产品中提取。
- 随着铟生产技术的不断改进,原料来源也呈现多元化的趋势,钢厂烟灰、铜冶炼渣、铅冶炼渣都开始成为提炼铟的原料。
- 目前,从铅、锌冶炼副产品中回收铟的工艺已经成熟,日本和韩国以再生铟为主。而再生铟产量比例已接近铟总产量的一半(USGS 2012)。日本对铟的消耗量已站全球需求的60%,尽管对铟的回收率达到了70%,但仍有27%被放弃,而直接用于电路的更是不足3%。按照目前的使用状况,即使进一步提高回收率,即使铟的消耗量中有一半使用替代材料,到2018年前后,纯粹的铟资源也将枯竭,最迟也就是在2025年。因此,首要摆在我们面前的问题是如何直接从含铟的铅矿、锌矿等矿石中,在提取主体金属铅、锌等金属的同时富集铟,使矿石的冶炼过程达到实际意义的综合目的,而非仅仅从冶炼的副产品中回收铟,这样可以大幅度的降低生产成本,提高经济效益。
- 以下是国外对于从LCD废料中回收铟的简易循环图
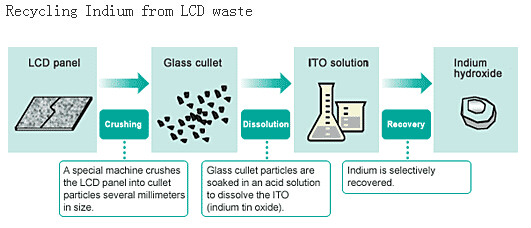
- 将LCD操作面板首先碎成小片状,溶解在酸溶液中,铟的氢氧化物被回收出来 。它是一个简单的操作过程,其中使用的化学物质简单,不需要大型能源支出(如需要实现高温或高压力)。
- 目前,世界上铟生产的主要提取工艺和主流提取工艺技术就是萃取-电解法。
- 其原则工艺流程是:含铟原料→富集→化学溶解→净化→萃取→反萃取→锌(铝)置换→海绵铟→电解精炼→精铟。
- 世界上铟产量的90%来自铅锌冶炼厂的副产物。铟的冶炼回收方法主要是从铜、铅、锌的冶炼浮渣、熔渣及阳极泥中通过富集加以回收。根据回收原料的来源及含铟量的差别,应用不同的提取工艺,达到最佳配置和最大收益。常用的工艺技术有氧化造渣、金属置换、电解富集、酸浸萃取、萃取电解、离子交换、电解精炼等。当前较为广泛应用的是溶剂萃取法,它是一种高效分离提取工艺。离子交换法用于铟的回收,还未见工业化的报导。在从较难挥发的锡和铜内分离铟的过程中,铟多数集中在烟道灰和浮渣内。在挥发性的锌和镉中分离时,铟则富集于炉渣及滤渣内。
- 在ISP炼铅锌工艺中,精矿中的铟较大部分富集于粗锌精馏工序产出的粗铅中,回收富铟粗铅的铟,一直采用碱煮提铟工艺,存在生产能力小、生产成本高、金属回收率低等缺点。
- 为了简化铟的提取流程,降低生产成本,提高金属回收率,针对原有的提铟生产工艺,本项目通过条件试验、循环实验及综合试验,研究开发了"富铟粗铅电解-铅电解液萃铟"提取工艺,确定了新工艺的最佳工艺参数。工艺流程为:粗铅熔化铸成极板,装入电解槽通电进行电解,阳极中的铟溶解进入电解液,当铟富集到一定浓度后,抽出电解液进行萃取、反萃,富铟反萃液经pH调节、置换、压团熔铸后得到粗铟。
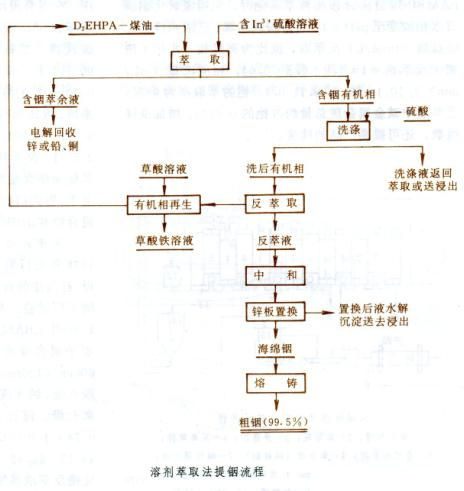
- 以富含铟、锗、镓的锌浸出渣为原料,经浸出、用丹宁沉淀锗和溶剂革取提取铟、锗、镓的过程。主要包括预处理、提取铟和提取镓等作业。该法于1975年在中国研究成功,此法中提取铟这部分的工艺已经用于工业生产,工艺流程如下图。
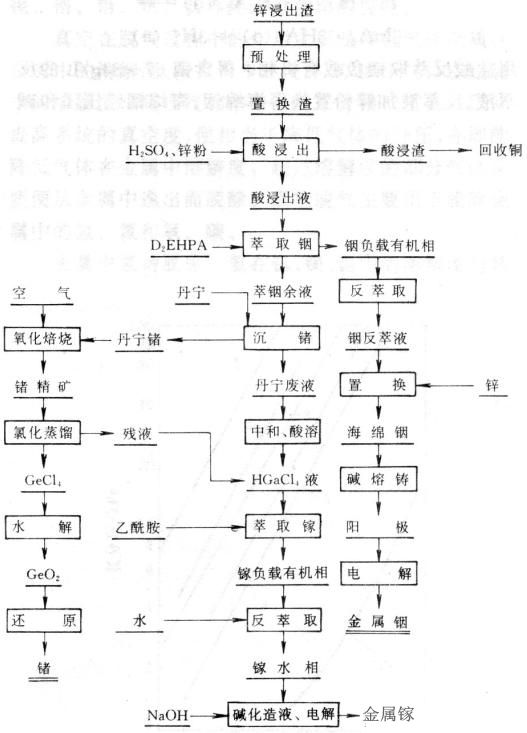
- 预处理湿法炼锌厂产出的锌浸出渣中,大部分锌和铁形成铁酸锌(nZnO•mFe2O3),而95%左右的铟、锗、镓以类质同象存在于铁酸锌。
- 用锌电解废液浸出含铟、锗、镓的锌浸出渣时,铟、锗、镓转入浸出液。过滤所得的滤液加锌粉置换,铟、锗、镓被置换成金属,获得富含铟、锗、镓置换渣。置换渣用硫酸逆流浸出,控制浸出液最终酸度含游离酸0.6mol/L左右,便可使置换渣中96%~l00%的铟、锗、镓转入溶液,反应为:
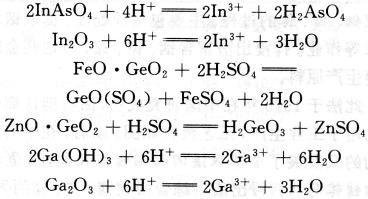
- 提取铟用D2EHPA(以H2A2表示)萃取液中的铟:
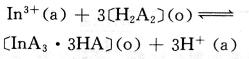
- 用盐酸反萃取铟负载有机相,得含铟67~84g/L的反萃液。反萃液加锌粉置换得海绵铟。海绵铟经压团和碱熔铸后送电解,得纯度99.99%的铟。铟的回收率超过90%。
- 分离提取铟的几种新技术包括液膜分离回收铟、螯合树脂分离回收铟、浸渍树脂分离技术回收铟和微胶囊技术回收铟。
- 在合适的条件下,运用这些技术可对铟进行有效地分离回收。这些新技术为分离回收铟提供了新的选择。
-
-
介绍
-
历史发展
-
性质
-
冶炼工艺
-
分类
-
应用
-
资源分布
-
行业政策
-
健康影响
-
行业标准
-
名企
-
推荐
-
- |
-
- |
-
- |
-
- |
-
- |
-
- |
-
- |
-
- |
-
- |
-
- |
-
- |
-
- |
-
- |
-
-
关于我们
联系我们
意见反馈
- 本站为公益性网站,旨在传播金属行业知识,为用户提供参考、借鉴和交流之用。知识内容整理秉承“新、全、专”原则,尽量为用户提供最可靠的知识信息。内容如有侵权请及时联系我们删除。