1948年美国研制出锗晶体管,使锗在半导体领域中获得重要地位。20世纪50年代,美国建设了世界第一个锗厂,60年代比利时建设的锗厂是世界上设计规模最大的锗生产企业,月生产金属锗6吨。美国主要从锌锗渣中提锗,英国主要从含锗烟尘中回收锗。
- 中国锗厂设计始于1959年。1963年开始以锗精矿为原料生产锗单晶。至1990年底,中国设计的锗生产厂(或车间)有8家,上海冶炼厂锗分厂主要从锗废料中回收锗,会泽铅锌矿锗车间主要从铅锌矿中提取锗。
- 目前锗厂所采用的原料有煤燃烧产出的含锗烟尘、重有色金属冶炼过程中回收的锗精矿和半导体器件生产中产出的含锗废料等。
- 锗精矿制取有火法、湿法和联合流程,根据不同的原料选定。从煤中提锗采用火法富集,重有色金属冶炼过程中回收锗采用湿法处理富集,半导体器件生产中产出的含锗废料,经预处理后直接加入到金属锗制取过程中。火法富集流程短、无腐蚀,但回收率低;湿法处理回收率高、精矿品位亦高,但流程长,化工试剂耗量多。
- 金属锗制取主要包括化学处理及精制,还原制取金属锗和物理提纯。先将锗的富集物用浓盐酸氯化,制取四氯化锗,再用盐酸溶剂萃取法除去主要的杂质砷,然后经石英塔两次精馏提纯,再经高纯盐酸洗涤,可得到高纯四氯化锗,用高纯水使四氯化锗水解,得到高纯二氧化锗。一些杂质会进入水解母液,所以水解过程也是提纯过程。纯二氧化锗经烘干煅烧,在还原炉的石英管内用氢气于650-680℃还原得到金属锗。
- 锗生产原则工艺流程示意图如下:
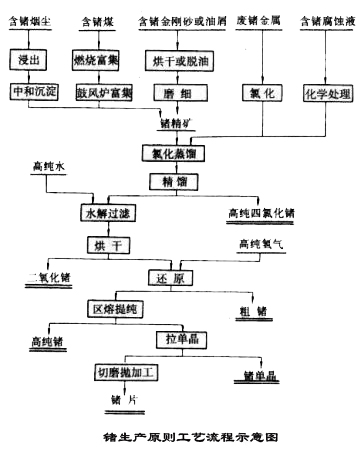
- 1. 富集
- 富集回收:锗的制取第一步是从重有色金属冶炼过程回收锗的富集物。
- 如果原料的品位不高,为了节约成本,一般要先进行富集才能进行生产。目前国内以回转窑富集方法的较多,用煤生产锗的一般用煤发电,回收布袋尘、旋风尘,再进行富集得到要求的品位。也有少部分用萃取方法的,萃取的厂家有株冶、南京锗厂。
- 以炼锌为例:
- 在火法炼锌过程中,锌精矿首先经过氧化焙烧,然后加入还原剂和氯入钠,在烧结机上烧结焙烧,锗以氯化物或氧化物形态挥发进入烟尘。如不采用氯化烧结措施,锗将富集于最后锌蒸馏的残留物中。
- 在湿法炼锌过程中,如锌精矿含锗不高时,大部分锗在硫酸浸出渣中,小部分锗进入溶液。在锌溶液净化过程中,由于锗的亲铁性质,氢氧化铁沉淀时吸附锗,锗进入铁渣。锌溶液用锌粉置换镉时,残留的锗和镉同时为锌粉所置换。如将浸出渣熔化,然后用烟化炉挥发铅、锌,则锗以一氧化锗状态挥发,富集于烟尘中。烟化炉可用来处理含锗的氧化铅、锌矿。将氧化矿在鼓风炉内熔炼,再用烟化炉处理炉渣挥发锗,挥发率大于90%。现代炼锌多用湿法,在处理含锗较高的硫化锌精矿(含锗100~150克/吨)时,首先使锗富集于浸出渣中,用烟化炉处理,烟尘含锗0.1%,用酸浸出,溶液净化后,加丹宁(C76H52O46)沉淀,沉淀物中含锗3~5%;经烘干、煅烧,得到含锗15~20%的锗灰,作为提锗原料。
- 2. 蒸馏
- 蒸馏是利用四氯化锗的沸点较低,约84摄氏度,将锗蒸馏出来达到分离的效果。
- 3. 精馏
- 四氯化锗,再用盐酸溶剂萃取法除去主要的杂质砷,此名叫复蒸。然后经石英塔精馏提纯,得到高纯四氯化锗。用高纯水使四氯化锗水解,得高纯二氧化锗(GeO2)。一些杂质会进入水解母液,所以水解过程也是提纯过程。水解母液中的锗可以返回进行盐酸蒸馏。
- 4. 还原
- 纯二氧化锗经烘干煅烧,在还原炉的石英管内用氢气于650~680℃还原得到金属锗。还原终结时可逐渐升温至1000~1100℃,使锗熔化,然后慢慢冷却,得到锗锭。还原时间一般为24小时,时间比较长,既浪费时间又消耗大量的电供热,针对上面的现象,国内发明了连续还原炉,目前在南京锗厂和驰宏锌锗使用。在生产中为了节省时间,采取了以下办法:
- 1、在冷却过程中使用风机对着炉子吹,可以是很有效的降低温度。
- 2、在还原结束后,直接升温熔化,可以减少慢慢升温的时间。
- 总的趋势还是要使用连续还原炉。
- 以上方法生产的锗锭只有5个九,电阻率在10左右,远不能满足科研和生产的需要,必须进行区域熔炼。
锗单晶的制备方法有两种:一种是直拉法,另一种是区熔匀平法。
- ①直拉法是将锗锭置于坩埚中熔化,然后用一固定在拉杆上的锗晶体作籽晶,垂直浸入温度略高于熔点的熔融锗中,以一定的速度从熔体向上拉出,熔融锗便按籽晶的结晶方向凝固。通过控制拉速、坩埚和籽晶转速等措施,以及自动控制炉温和单晶直径等技术,可以制成n型电阻率为 0.003~40欧姆•厘米、p型电阻率为0.002~40欧姆•厘米、位错密度为500~3000厘米-2、直径为20~300毫米的锗单晶。
- ②区熔匀平法所用的炉子为水平式石英管加热炉,能生产电阻率均匀的锗单晶,电阻率的径向均匀度为±3%,纵向均匀度为±7%,位错密度为103厘米^-2,单晶截面为5~12厘米^2。
- 根据美国地质调查局2014年发布数据显示,全球锗总消费量的30%来源于回收材料。下面具体介绍了加工废料中锗的回收和锌冶炼工艺中锗的回收:
- 加工废料中锗的回收
- 从锗加工废料中回收锗非常重要。自冶炼到制成锗晶体管整个过程,特别是区熔提纯、拉制单晶、切片、磨片和抛光锗片的加工过程中,会产生大量的含锗废料。这些废料的含锗量为:切割粉60~70%,碎片80~90%,滤纸20%,腐蚀液2~10%。
- 从废料中回收锗的方法很多,主要有:①用氯气在石英容器内,使锗氯化成四氯化锗,然后蒸馏回收;②用新鲜的NaOCl于80℃处理锗残渣,生成锗酸钠(Na2GeO3),然后加入氢氧化铵,生成锗的沉淀物 (Na2O)x(NH4)yGe2O3,回到四氯化锗生产流程。在处理含氢氟酸的腐蚀液时,加入氢氧化铵,可生成氟化铵和锗酸铵(NH4)x Ge2O3沉淀。在四氯化锗水解过程中产生的水解液和洗涤液中含有少量(约6~7克/升)的锗,回收的方法是用硫酸镁和氢氧化铵使锗沉淀为正锗酸镁。
- 锌冶炼工艺中锗的回收
- 我国锌冶炼采用的主要工艺分为火法和湿法两类,其中火法主要为ISP(铅锌密闭鼓风炉熔炼法),湿法有常规法、热酸浸出法。由于冶炼工艺的不同,锗的富集过程和后续处理工艺也不尽相同,且各具特点。
- 1. ISP工艺中锗的回收
- ISP炼锌过程中,锗主要分布在硬锌中,约42%. 某厂经过多次技术改造,其铟、锗综合回收的工艺流程图如下:
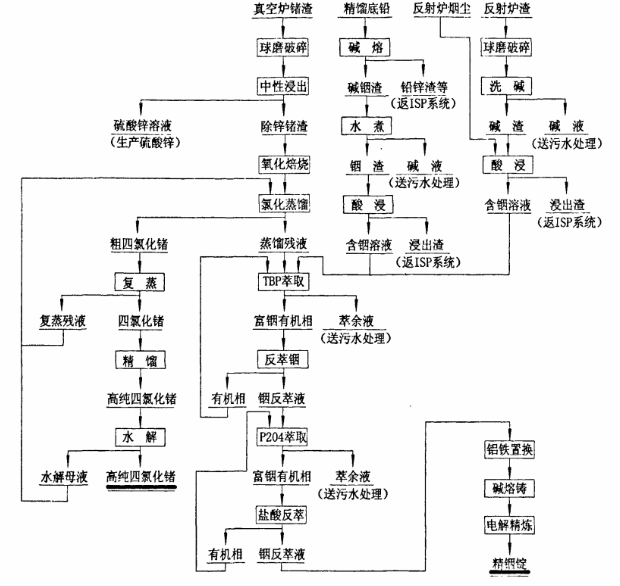
- 虽然在ISP火法炼锌工艺中,铟、锗等金属均能得到回收,但在主流程中较分散,故富集、回收流程长,且进入密闭鼓风炉前床渣中的铟和锗在烟化炉熔炼时难以回收,因此,铟和锗回收率均不高,其直收率分别为50%和30%-40%。
- 2. 常规法炼锌工艺中,由于锗大部分损失在窑渣中,锗的回收率低于30%。
- 3. 热酸浸出-黄钾铁矾法炼锌工艺中锗的富集回收。
- 在热酸浸出-黄钾铁矾法炼锌工艺中,锌焙砂中性浸出渣用高温、高酸浸出,可进一步提高锌铟锗的浸出率,使锌、铟浸出率均可达到98%,锗的浸出率约92%。热酸浸出液含铁较高,用黄钾铁矾法沉铁,约95%的铟、10%的锗一起沉淀进入铁矾渣,沉矾后液再中和水解沉锗,溶液中锗进入锗铁渣到富集。
- 某厂从锗铁渣中富集锗,采用锗铁渣酸浸-丹宁沉锗工艺,丹宁锗渣经洗涤、脱水、干燥后灼烧得到锗精矿。锗铁渣酸浸时,温度控制75摄氏度左右、浸出时间1.5小时、终酸PH值为1.5-2,锗浸出率为74%。浸出渣含锗较高,仍需返回主流程中:丹宁沉锗是富集锗精矿的传统工艺,把温度控制在60-75摄氏度、沉淀时间20-30分钟,锗沉淀率为96%-99%,但丹宁沉锗需消耗大量的丹宁酸,一般为锗量的25-45倍,且丹宁会对锌电积时的电流效率产生不良影响。在锗铁渣富集锗的工艺过程中,锌精矿至锗精矿的锗直收率约50%-55%。
-
-
介绍
-
性质
-
历史发展
-
应用
-
提取工艺
-
健康影响
-
资源分布
-
行业政策
-
名企
-
推荐
-
关于我们
联系我们
意见反馈
- 本站为公益性网站,旨在传播金属行业知识,为用户提供参考、借鉴和交流之用。知识内容整理秉承“新、全、专”原则,尽量为用户提供最可靠的知识信息。内容如有侵权请及时联系我们删除。