一、湿法生产工艺(属淘汰工艺):以酸级萤石粉、浓硫酸和氢氧化铝为原料,先将酸级萤石粉与浓硫酸反应生成的氟化氢气体用水吸收,得到含量为30%的有水氢氟酸,使之再与氢氧化铝进行液-固混合相反应,得到过饱和的氟化铝溶液,经过结晶、过滤、高温煅烧脱水,最终得到氟化铝产品。其化学反应方程式如下:
CaF2+H2SO4→CaSO4+2HF↑
3HF+Al(OH)3→AlF3·3H2O
AlF3·3H2O→AlF3+3H2O
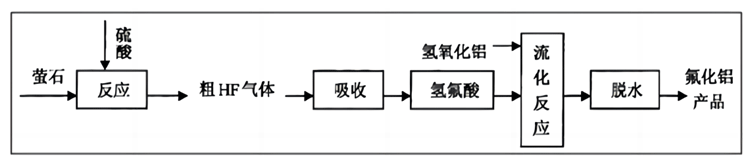
此项工艺在制备30%的氢氟酸过程中,氟化氢气体中的杂质也一并被吸入溶液中,致使氢氟酸中含有较多的硫酸、磷酸、氟硅酸、亚硫酸等杂质。这些杂质会与氢氧化铝发生副反应。生成的产物以吸附或夹晶的方式混杂在氟化铝晶体之中,极大地影响最终产品的质量。同时,由于后期煅烧脱水处理时,结晶水从晶体中除去会导致晶格破碎,粒度降低,使得氟化铝松装密度较低(0.7g/cm3),产品最终含水量也较高(≥3%)。因此,湿法氟化铝含量低,杂质多,水分含量高,堆密度低,流动性差。基本上不适应现代电解槽使用。
二、干法生产工艺:与湿法一样,也以酸级萤石粉、浓硫酸和氢氧化铝为原料,有所不同的是,工艺流程中第一步所产生的氟化氢气体要经过气相净化系统,除去所含的粉尘和硫酸,然后再与干燥的氢氧化铝(含水量12%)混合,送入双层流化床中完成焙烧脱水与氟化两步反应,并最终制得氟化铝产品。其化学反应方程式如下:
CaF2+H2SO4→CaSO4+2HF↑
3HF+Al(OH)3→AlF3+3H2O

该工艺属于第二代氟化铝生产技术。使用经过简单除尘、除酸处理过的氟化氢气体(90%)与氢氧化铝进行反应,其氟化氢气体杂质含量较湿法氟化铝工艺相比低。而且,在干法氟化铝反应流化床反应器中,由于反应温度高、气相反应物流速快,使得气态杂质与水生成的硫酸、亚硫酸、磷酸等没有足够的时间与氢氧化铝发生副反应,因此其最终氟化铝产品中的杂质含量比湿法氟化铝要低。该方法是我国现阶段应用最广泛、技术最为成熟的氟化铝生产工艺。但是,这种工艺存在下列缺点:(1)污水的排放量比较大,且污水中所含的氢氟酸、氟硅酸不能被综合利用,只能排入污水处理站,造成总处理成本较高;(2)技术设计上还存在部分工艺及设备设计比较复杂或欠合理等问题,致使实际开车生产过程中设备运行及维护成本较高。
三、无水生产工艺:无水法氟化铝无水制备工艺可以分为两大部分,即无水氟化氢的制备部分和氢氧化铝的氟化部分。与湿法氟化铝和干法氟化铝工艺一样,该方法也是以酸级萤石粉、浓硫酸和氢氧化铝为原料。与前两种方法所不同的是,此工艺中前两种反应原料生成的氟化氢粗气,经过了冷凝、精馏为纯度99.9%以上的液态无水氟化氢的精制步骤。高纯度的氟化氢与氢氧化铝(含水量6%)在循环流化床中的反应过程几乎没有副反应发生,从而极大地降低了最终氟化铝产品的杂质含量。同时,由氢氧化铝原料本身含水量较低,在投料前无需额外的煅烧脱水过程,减少了晶体破裂的可能性,也使得最后得到的产品具有松装密度大(1.6g/cm3)、含水量低等优点。其化学反应方程式如下:
CaF2+H2SO4→CaSO4+2HF↑
3HF+Al(OH)3→AlF3+3H2O
该工艺是21世纪初我国国内氟化工企业自主研发出来的第三代制备技术。与湿法氟化铝和干法氟化铝工艺相比,有最为优异的最终产品质量,属于目前我国国内最为先进的氟化铝生产技术。
四、氟硅酸法工艺:氟硅酸法又称磷肥副产法。该方法利用磷肥生产企业产生的含氟废气,四氟化硅和氟化氢,经过二次循环吸收后制得氟硅酸溶液(含H2SiF615%、P2O5<0.25g/L),将其与氢氧化铝浆料(Al2O3干基≥64%)混合反应,将所得的氟化铝溶液通过过滤,除去硅胶沉淀物后,结晶、离心分离制得三水氟化铝滤饼,最后经过干燥、煅烧脱水处理,制得最终产品。其化学反应方程式如下:
H2SiF6+2Al(OH)3→2AlF3+2SiO2+4H2O
AlF3·3H2O→AlF3+3H2O。

上述工艺虽然先进,但缺点是:①工艺条件要求苛刻;②投资大;③硅元素未被利用,SiO2以渣排放;④要求氟硅酸的w(H2SiF6)大于18%,低浓度氟硅酸不适用。
在此基础上开发了一种新工艺:采用氟硅酸与碳酸氢铵反应生成氟化铵溶液和二氧化硅沉淀,分离后,滤饼经洗涤、干燥得白炭黑;氟化铵溶液与六水氯化铝反应得可溶性α-AlF3·3H2O和氯化铵溶液,在合适的工艺条件下,可溶性α-AlF3·3H2O转化成不溶性β-AlF3·3H2O,经分离、洗涤、干燥、煅烧得氟化铝成品;分离后的溶液经蒸发、结晶、干燥后得氯化铵副产品。其中化学反应式如下:
H2SiF6+6NH4HCO3→6NH4F+SiO2↓+6CO2↑+4H2O
H2SiF6+2NH4HCO3→(NH4)2SiF6+2CO2↑+2H2O
(NH4)2SiF6+4NH4HCO3→6NH4F+SiO2↓+4CO2↑+2H2O
3NH4F+AlCl3·6H2O→α-AlF3·3H2O+3NH4Cl+3H2O
α-AlF3·3H2O→β-AlF3·3H2O

CaF2+H2SO4→CaSO4+2HF↑
3HF+Al(OH)3→AlF3·3H2O
AlF3·3H2O→AlF3+3H2O
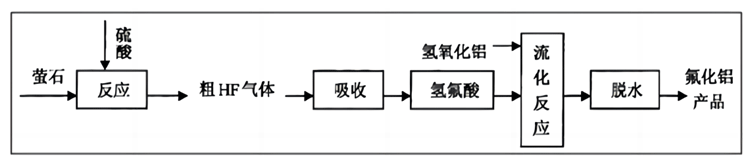
此项工艺在制备30%的氢氟酸过程中,氟化氢气体中的杂质也一并被吸入溶液中,致使氢氟酸中含有较多的硫酸、磷酸、氟硅酸、亚硫酸等杂质。这些杂质会与氢氧化铝发生副反应。生成的产物以吸附或夹晶的方式混杂在氟化铝晶体之中,极大地影响最终产品的质量。同时,由于后期煅烧脱水处理时,结晶水从晶体中除去会导致晶格破碎,粒度降低,使得氟化铝松装密度较低(0.7g/cm3),产品最终含水量也较高(≥3%)。因此,湿法氟化铝含量低,杂质多,水分含量高,堆密度低,流动性差。基本上不适应现代电解槽使用。
二、干法生产工艺:与湿法一样,也以酸级萤石粉、浓硫酸和氢氧化铝为原料,有所不同的是,工艺流程中第一步所产生的氟化氢气体要经过气相净化系统,除去所含的粉尘和硫酸,然后再与干燥的氢氧化铝(含水量12%)混合,送入双层流化床中完成焙烧脱水与氟化两步反应,并最终制得氟化铝产品。其化学反应方程式如下:
CaF2+H2SO4→CaSO4+2HF↑
3HF+Al(OH)3→AlF3+3H2O

该工艺属于第二代氟化铝生产技术。使用经过简单除尘、除酸处理过的氟化氢气体(90%)与氢氧化铝进行反应,其氟化氢气体杂质含量较湿法氟化铝工艺相比低。而且,在干法氟化铝反应流化床反应器中,由于反应温度高、气相反应物流速快,使得气态杂质与水生成的硫酸、亚硫酸、磷酸等没有足够的时间与氢氧化铝发生副反应,因此其最终氟化铝产品中的杂质含量比湿法氟化铝要低。该方法是我国现阶段应用最广泛、技术最为成熟的氟化铝生产工艺。但是,这种工艺存在下列缺点:(1)污水的排放量比较大,且污水中所含的氢氟酸、氟硅酸不能被综合利用,只能排入污水处理站,造成总处理成本较高;(2)技术设计上还存在部分工艺及设备设计比较复杂或欠合理等问题,致使实际开车生产过程中设备运行及维护成本较高。
三、无水生产工艺:无水法氟化铝无水制备工艺可以分为两大部分,即无水氟化氢的制备部分和氢氧化铝的氟化部分。与湿法氟化铝和干法氟化铝工艺一样,该方法也是以酸级萤石粉、浓硫酸和氢氧化铝为原料。与前两种方法所不同的是,此工艺中前两种反应原料生成的氟化氢粗气,经过了冷凝、精馏为纯度99.9%以上的液态无水氟化氢的精制步骤。高纯度的氟化氢与氢氧化铝(含水量6%)在循环流化床中的反应过程几乎没有副反应发生,从而极大地降低了最终氟化铝产品的杂质含量。同时,由氢氧化铝原料本身含水量较低,在投料前无需额外的煅烧脱水过程,减少了晶体破裂的可能性,也使得最后得到的产品具有松装密度大(1.6g/cm3)、含水量低等优点。其化学反应方程式如下:
CaF2+H2SO4→CaSO4+2HF↑
3HF+Al(OH)3→AlF3+3H2O
该工艺是21世纪初我国国内氟化工企业自主研发出来的第三代制备技术。与湿法氟化铝和干法氟化铝工艺相比,有最为优异的最终产品质量,属于目前我国国内最为先进的氟化铝生产技术。
四、氟硅酸法工艺:氟硅酸法又称磷肥副产法。该方法利用磷肥生产企业产生的含氟废气,四氟化硅和氟化氢,经过二次循环吸收后制得氟硅酸溶液(含H2SiF615%、P2O5<0.25g/L),将其与氢氧化铝浆料(Al2O3干基≥64%)混合反应,将所得的氟化铝溶液通过过滤,除去硅胶沉淀物后,结晶、离心分离制得三水氟化铝滤饼,最后经过干燥、煅烧脱水处理,制得最终产品。其化学反应方程式如下:
H2SiF6+2Al(OH)3→2AlF3+2SiO2+4H2O
AlF3·3H2O→AlF3+3H2O。

上述工艺虽然先进,但缺点是:①工艺条件要求苛刻;②投资大;③硅元素未被利用,SiO2以渣排放;④要求氟硅酸的w(H2SiF6)大于18%,低浓度氟硅酸不适用。
在此基础上开发了一种新工艺:采用氟硅酸与碳酸氢铵反应生成氟化铵溶液和二氧化硅沉淀,分离后,滤饼经洗涤、干燥得白炭黑;氟化铵溶液与六水氯化铝反应得可溶性α-AlF3·3H2O和氯化铵溶液,在合适的工艺条件下,可溶性α-AlF3·3H2O转化成不溶性β-AlF3·3H2O,经分离、洗涤、干燥、煅烧得氟化铝成品;分离后的溶液经蒸发、结晶、干燥后得氯化铵副产品。其中化学反应式如下:
H2SiF6+6NH4HCO3→6NH4F+SiO2↓+6CO2↑+4H2O
H2SiF6+2NH4HCO3→(NH4)2SiF6+2CO2↑+2H2O
(NH4)2SiF6+4NH4HCO3→6NH4F+SiO2↓+4CO2↑+2H2O
3NH4F+AlCl3·6H2O→α-AlF3·3H2O+3NH4Cl+3H2O
α-AlF3·3H2O→β-AlF3·3H2O

- 热门推荐
产品推荐