- 目前, 世界上从矿石中提取氧化铍的仅有中国(如水口山六厂)、 美国的布拉什威尔曼公司和哈萨克斯坦的乌尔宾斯基冶金工厂等为数不多的数家企业,主要的生产方法为硫酸法和氟化法。
- 硫酸法仍是现代氢氧化铍与氧化铍生产中广泛应用的方法之一,其原理是利用预焙烧破坏铍矿物的结构与晶型,再采用硫酸酸解含铍矿物,使铍、铝、铁等酸溶性金属进入溶液相,与硅等脉石矿物初步分离,然后将含铍溶液进行净化除杂,最终得到合格的氧化铍(或氢氧化铍)产品。
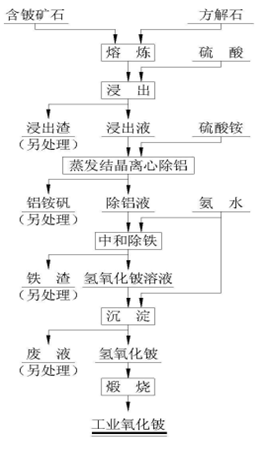
- 早在20世纪40年代, 德国德古萨公司就采用硫酸法(即德古萨工艺) 流程生产氢氧化铍。随后,美国布拉什铍公司对该流程进行了改进(即Brush工艺),1969 年美国布拉什-威尔曼公司建成了一家结合萃取技术(即酸浸 -萃取工艺)处理低品位硅铍石与绿柱石的工厂。至今,硫酸法已经过了不断改进和完善。
- 德古萨工艺适合于处理含铍较高的绿柱石矿物。由于绿柱石不能直接被硫酸分解,必须加入碱熔剂或经热处理改变其晶型或结构,增加反应活性后才能酸解,其反应为:

- 加入的熔剂可以为碱性氧化物如纯碱、石灰等,也可以为氯化物如氯化钙、 氯化钠等。其中,石灰具有价格与环保优势,焙烧时配料比(m石灰/m绿柱石 )通常控制为1~3,焙烧温度一般为1400~ 1500℃。
- Brush 工艺免除了添加熔剂步骤, 直接将绿柱石在电弧炉中加热到1700℃熔化, 然后倾入高速流动的冷水中, 得到粒状的铍玻璃,再在煤气炉中加热至900℃ 使氧化铍析出, 粉碎后与 93%的硫酸混合成浆状,将料浆于 250~ 300℃下酸解, 矿石中铍的浸出率可以达到93%~ 95%, 过程的主要反应如下:
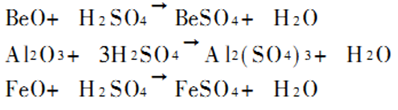
- 美国矿物局于20世纪60年代采用酸浸-萃取工艺处理犹他州的硅铍石和北卡罗来那州金斯山的绿柱石。1969年, 美国布拉什 -威尔曼公司在犹他州的德尔塔建立了用硫酸 -萃取工艺处理低品位硅铍石的工厂,所采用的原理如下图:
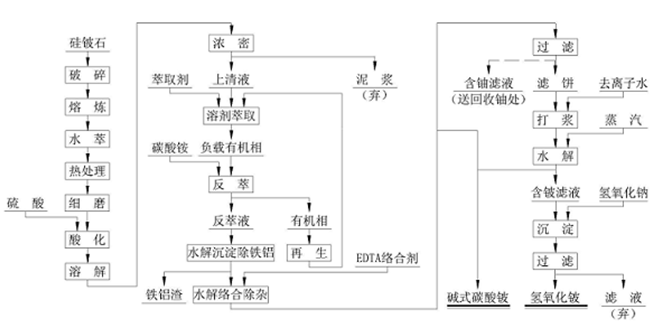
- 硅铍石首先经粉碎焙烧,将焙炒破碎(为避免粉尘飞扬而用水喷淋)后在带分级机的球磨机中湿磨至<0.07mm,喷淋和湿磨均采用逆流倾注洗涤浓密机的洗水。湿磨后往矿浆中加入10%的硫酸,在液固比为3及温度65℃的条件下搅拌酸浸24h,然后再在逆流倾注洗涤浓密机中逆流沉降,弃去泥浆,所得浸出液含铍0.4~0.7g/ L、铝4~7g/L,pH 值为0.5~1.0。以膦酸二(2-乙基己基)酯(D2EHPA)-乙醇 -煤油作为有机相进行八级逆流萃取,铍及少量铝、铁进入有机相萃余液废弃。该萃取过程的反应式为:

- 获得的负载有机相用碳酸铵溶液反萃,铍进入水相中形成铍碳酸铵,铁、铝也进入水相,反萃过程的反应式为:

- 反萃后的有机相经硫酸酸化再生后返回萃取工序,反萃液则加热至70℃,使铁、铝水解沉淀而分离;再将除铁、铝后的溶液加热至95℃,并且加入EDTA络合剂,使铍碳酸铵溶液水解得到碱式碳酸铍沉淀,过滤后的含铀滤液用于回收铀,而滤饼则用去离子水打浆后再用蒸汽加热至 165℃水解,主要反应如下;
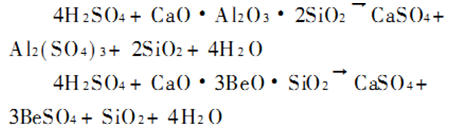
- 水解得碱式碳酸铍沉淀和含铍滤液,滤液加碱后沉淀出氢氧化铍,与碱式碳酸铍一同作为产品。酸浸-萃取工艺具有如下特点:有机相及反萃沉淀均可返回利用,效率较高;排出的污染物除浸出渣外,只有萃余液和酸洗废液,数量少易于处理;萃取与反萃过程易实现连续化、自动化;可处理杂质锂、氟含量高的矿石并获得质量好的氧化铍产品。
- 水口山六厂所采用的提铍生产流程为改进的德古萨工艺。该厂于1958 年开始铍的生产,是国内主要的铍冶炼厂,素有”中国铍业一枝花“之称。该厂以绿柱石为原料提取氧化铍,经过40 多年的实践,工艺日趋完善,具体流程如下:

- 将绿柱石与方解石经配料混合,装入电弧炉,在1400~1500℃下进行熔炼,熔体经水淬,成为高反应活性的铍玻璃体,其反应为:

- 湿磨后的细铍玻璃与浓硫酸混和后,剧烈反应可使温度升至250℃左右,过程中硅酸脱水,析出SiO2,然后用水浸取,液固分离后得到含铍的浸取液,过程主要反应如下:
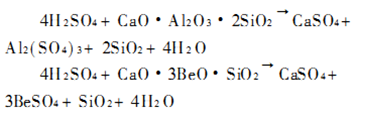
- 浸出液中含铁、铝等杂质,经浓缩后,添加硫酸铵,再冷却结晶,铁、铝形成硫酸亚铁铵和硫酸铝铵矾渣,液固分离后得到含铍的除铝液,过程主要反应如下:
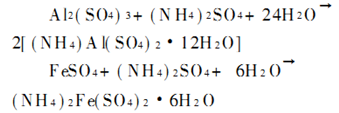
- 往除铝液中加入氧化剂,以氨水作中和剂,调节pH值为5左右沉淀铝、铁,其反应如下:
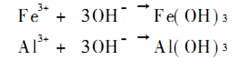
- 液固分离后得到含铍的中和液。用氨水调节中和液的pH值至7.5,氢氧化铍即从溶液中完全沉淀,所含的少量杂质铝可通过碱洗进一步分离,其反应如下:

- 将氢氧化铍煅烧即得到氧化铍,其反应为

- 此工艺由德国德古萨工艺改进而来,虽然流程较长,但金属回收率、产品质量较高,化工原料均廉价易得,因此具有成本较低的优点。
- 氟化法建立在铍氟酸钠能溶于水,而冰晶石不溶于水的原理之上。将绿晶石与硅氟酸钠混合,于750℃下烧结2h,烧结块经湿磨至粒径为0.074mm,室温下用水三次浸出,其主要反应如下:
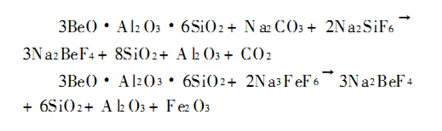
- 氟化法获得的浸出液比硫酸法的纯度高,不需要专门的净化处理就可以直接用氢氧化钠沉淀出氢氧化铍,其反应为:

- 过滤氢氧化铍后的滤液中含有NaF需进行回收,先用硫酸调节滤液的pH值至4,在不断搅拌的情况下加入硫酸铁,以得到铁氟酸钠(可将其返回烧结配料),其反应为:

- 氟化法的流程比较简单,防腐蚀条件好,并且还适合处理含氟高的原料,但产品质量稍逊于硫酸法。但该法处理低品位矿时,除辅助剂耗量增加外,钙和磷的增加将降低烧结料中水溶铍的含量,影响回收率,且三废处理时还带来氟处理的问题。
- 金属铍内部含有大量的空隙,显微研究表明为粗大的晶粒结构,即使加工处理后,晶粒度也大于100μm,结果铍铸锭的强度性能不高,因此,铍件的制造只能采用粉末冶金法,即先将铍锭车削成屑,再制成粉末,最后团结成型。
- 铍粉末的化学成分、物理性能和工艺性能对其固结过程及最终产品性能有着重大的影响,旧有的粉化工艺已不能适应新一代高强度、高延性铍材的要求。铍工业的进步是与铍粉末冶金技术的发展紧密相连的。近二十年开始研究和应用的新的铍粉制取法是冲击研磨,又叫冷流冲击,是利用金属的冷脆性而发展起来的一种粉末生产新工艺,它是利用高速、高压气体带着较粗的颗粒通过喷嘴轰击在击碎室内的铍靶上,压力立刻从高压降到大气压。发生绝热膨胀,使铍靶和击碎室的温度降到室温甚至零度以下,此时,冷却了的颗粒经撞击即被粉碎 。 与传统的园盘磨和球磨法相比,该法具有粉末纯度高,粒形均匀,粉末内应力大,效率高, 成本低,有利于防护等优点。
- 此外,利用气体雾化生产铍粉也可制得规则的球形颗粒粉末,能够显著减少或消除坯块的各向异性,同时,球形粉末具有很好的流动性和较高的充填密度,从而得到几何尺寸精确的固结件,而且雾化铍粉的显微结构普遍呈多晶态,这对于随后的热等静压工艺尤为重要。
- 加压成形是铍粉末冶金的第二大工序。以前多采用真空热压,进入80年代真空热压铍材得到了进一步发展。通过改变化学成分、粒度分布及处理温度,已生产出各种性能不同、用途 广泛的镀产品。近二十年来迅速发展的一项新技术是热等静压技术,其产品的性能远优于真空热压,尤其是能生产出结构极复杂的异型铍部件和高强度延性铍材,而工艺效率又大为提高,是一种比较经济和具有发展前途的工艺。
-
-
介绍
-
历史发展
-
性质
-
资源储量
-
应用
-
提取工艺
-
健康影响
-
行业标准
-
名企
-
推荐
-
关于我们
联系我们
意见反馈
- 本站为公益性网站,旨在传播金属行业知识,为用户提供参考、借鉴和交流之用。知识内容整理秉承“新、全、专”原则,尽量为用户提供最可靠的知识信息。内容如有侵权请及时联系我们删除。